When should you choose labeling over printing for product and case coding?
Accurate and reliable product identification is essential for product and case coding. But what’s the best way to get the information onto the packaging? Should you choose labeling or marking?
Looking at dollars alone, directly printing marks on case is generally the most cost-effective option. It tends to offer higher maximum printing speeds and lower printing costs, thanks to reduced consumable expense.
But the decision is not that simple.
There are situations when labels are the only option for regulatory compliance, not to mention other situations when labeling leads to more precise and consistent results than marking.
While both methods have pros and cons, in this article, we will explore five situations when you should choose a labeling system over marking.
But first, some definitions.
What do we mean by labeling and marking?
The two most common product and case coding solutions are print-and-apply labeling and direct-to-case marking.
Print-and-apply labeling refers to a machine that prints information on the labels and applies those labels directly onto products and packaging, such as cases and pallets. The process is automated to apply a label to any side of a box or case, with software enabling operators to create and change labels easily. Look for reliability and simplicity in an automated print and apply labeling machine.
Direct-to-case marking is where codes are directly printed onto cases without the need for backing paper or labels. A number of marking technologies including thermal inkjet, piezo inkjet, and drop-on-demand valvejet, are viable options.
5 situations where you should choose labeling over marking
1. Your customers mandate that barcodes must be on print-and-apply labels
If you’re supplying products to large retailers, you might find their supplier standards specify that they only accept labels for case coding.
Fail to meet the specified standards, and you risk product rejection by retailers, which can damage your sales, customer relationships, and your bottom line.
Printing on certain substrates requires a specific print resolution and barcode quality, which print and apply labelers can consistently achieve. The high absorbency of cardboard means the print quality of ink is typically lower compared to labels. That’s why some retailers mandate that barcodes must be printed onto labels.
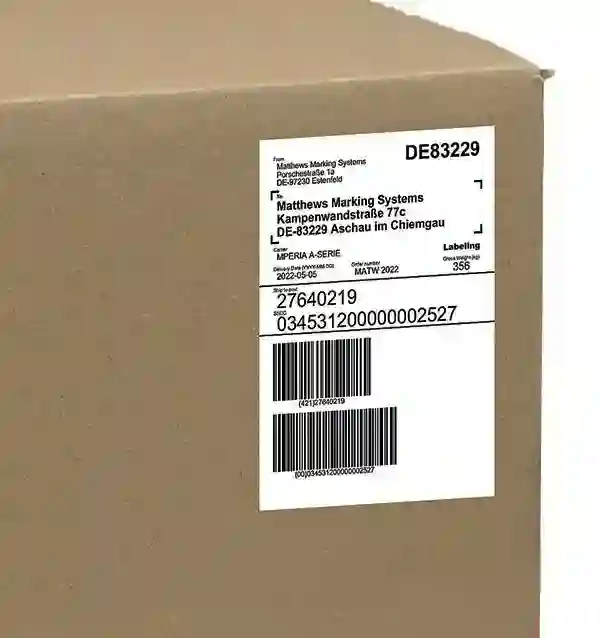
The use of labels may be a requirement imposed by some customers. If so, direct case printing isn’t an option.
2. You need flexibility and versatility for your production line
If you’re working with lots of products or planning to introduce new and different product lines, choosing a coding solution that can provide flexibility is critical.
This is where a print and apply labeling system delivers the goods. Labeling can be used for primary retail products through to wood, pipes, and steel.
With labeling, you have a wide choice of label stock, which means you can work with various products, materials, and shapes, including applying labels to flat, tapered, or round surfaces. You can also use pre-printed labels that include a small section for date and lot codes, eliminating the need for an additional printing step on your line.
In addition, the label and ribbon combinations can be easily adapted to the packaging substrate so you don’t have to upgrade your machine when changing your products or packaging. You can also choose from different label sizes depending on how much information is needed on the label.
Take international produce supplier 4Earth Farms. The company manages an enormous volume of produce SKUs to serve health food retailers and wholesalers worldwide. Their facility includes multiple production lines for various product and packaging needs. With the MPERIA A-Series print and apply labeling machine, they can quickly move the system from station to station, providing coverage across multiple production areas. The labeler features multiple applicators and configurations for virtually any production line.
3. You need to match to the contour of the packaging
If you have irregularly shaped products or surfaces, it might seem like direct marking would be easier. However, many printers struggle to apply codes to cases with inconsistent contours and curves.
Labeling machines are also adaptable and flexible. You can label your goods from above, below, and around edges and corners.
4. You need to provide precise information for traceability
Industries are on heightened alert regarding traceability requirements, and there is less and less tolerance for coding errors.
To ensure traceability of your products throughout the supply chain, you must comply with GS1 standards, which give retailers and suppliers guidelines on which machine-readable code is to be used and what quality of code is acceptable.
High-quality barcodes are non-negotiable, meaning labeling is the only option for many products.
Labeling allows for including a wide range of information, such as barcodes, expiration dates, and batch numbers, facilitating traceability throughout the supply chain. The key is looking for a label printer applicator, like the MPERIA A-Series, that boasts exceptional print quality to ensure labels fully comply with strict GS1 standards.
5. You need to provide information on multiple sides
A label printer applicator can print barcodes in the correct format for your case or product and then apply the label to multiple sides of the case.
It comes down to the applicators – label printers come with different applicator options that allow for flexibility of label application.
For example, the A-Series has the option of a wipe applicator, which can handle side, front, rear, or top placements and adjacent sides. It can also wrap a single label around carton corners in one smooth motion, which helps reduce the number of labels that need to be applied.
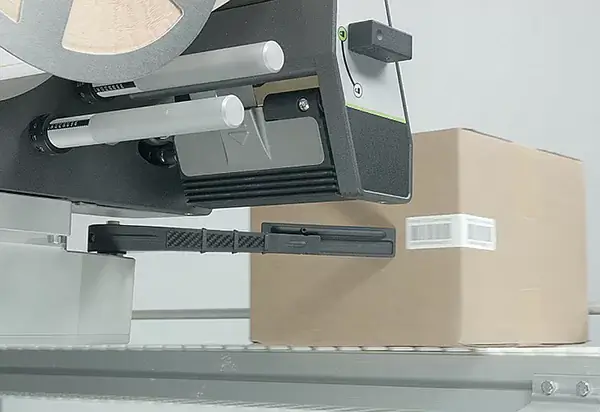
The A-Series Wipe90 applicator can wrap labels around corners, an important requirement in some applications.
Choosing the right labeling system for your situation
If you find yourself in any of the situations above, it’s time to get serious about a print and apply labeling system for your business.
The good news is that today’s automated labelers are designed with such efficiency and ease that print and apply labeling is nearly as efficient as marking, even if consumable costs remain somewhat higher.
The MPERIA A-Series print and apply labeling machine delivers excellent print quality and error-proof labels on every package, carton, and pallet, meaning your labels fully comply with strict retailer and industry standards.
The MPERIA controller and software allows operators to easily program the labeler on the production line – label updates and product changeovers have never been so fast. The easy-access design means changing printheads and label rolls can be done quickly without any tools, so your production lines never stay down for long. For example, a label change-out can be completed in as little as 20 seconds, and because the printhead is attached magnetically, replacement takes minutes instead of hours. Learn more about marking systems on our case printing and labeling page.
Ready to talk through your labeling needs?
Talk to our team and book your free onsite consultation and demo. Contact us on 800.775.7775 or fill out the quick form below.