This post is part two of our series on choosing the right ink for product marking. In Part 1: Understanding Ink to Drive Marking and Coding Success, we discussed what goes into ink composition and the many variables involved with selecting ink. This post examines common substrates and ink compositions that typically work together.
Most inks used in inkjet marking and coding applications are “complex” inks. That’s because inside each drop of ink is a complex makeup of solvents, resins, colorants, and additives, each with a specific role. Figuring out the best combination of ingredients for a particular application requires a combination of marking and coding knowledge and expertise coupled with extensive testing and refinement.
The ideal ink for a given application can vary greatly depending on the substrate, print technology, temperature, and other factors. Beyond basics like porous or non-porous substrates, variables that can impact ink selection include:
- If the ink needs to be permanent or removable, or invisible to the naked eye
- If there will be any residue on the product surface, such as oil, dust, wax, or a film or other coating
- The texture of the surface area (e.g., smooth or rough)
- The level of contrast needed
- Considerations of any surface color variations or inconsistencies Surface temperatures when marking on hot metal
- If there are any regulatory requirements, such as ink that is aerospace-approved or halogen-free
- Considerations of environmental factors when printing – for example, the level of moisture, temperature, and humidity in both the printing area and where the product will be stored
- If there is a possibility of exposure to scratching, abrasion, or other harsh conditions impacting mark durability
There is no “one ink fits all” approach to substrates
Because substrates – and every manufacturing environment — come with their own variations, there are no hard-and-fast rules about ink choice for every substrate or application. That said, we can provide insight into why different ink compositions may work better than others for five common substrates:
Cardboard
Corrugated cardboard, which comes in multiple colors beyond the typical brown, is often used for secondary packaging and requires large, easily readable marks. Cardboard is a porous surface, but it can have a waxy film or laminated layer, which will impact the type of ink required. For more porous cardboard, oil- or water-based inks may allow for increased absorption and faster dry time, whereas cartons with a glossier coating may require a solvent-based ink.
Metal
Aluminum vs. steel vs. coated metal (i.e. galvanized, anodized). Each type of metal or coating may respond differently to ink. Solvent-based or UV inks (that dry instantly when exposed to UV light) allow for greater durability and faster drying time, which is an important factor considering that metal is a non-porous substance. They also are more apt to resist fading and smudging.
Wood
This substrate spans everything from lumber to manufactured building products, each with its own composition, density, absorption rate, and porousness. Like cardboard, water-based inks may increase absorption and dry time, and UV inks can allow for fast curing and durability. However, an oil-based ink may be a better fit for rough or untreated surfaces, in most cases.
Rubber
Tires are a good example of a rubber product that requires clear and consistent marking as various rubber compositions move through manufacturing . Acetone-based inks with vinyl resins will typically perform well on rubber products. Solvent-based inks are also typically more resistant to water and abrasion.
Plastic bags
Given the wide variability in the substrates used for bags, it’s particularly important to test thoroughly. Inks that contain rosin ester resins are often well-suited for plastic products. As a non-porous substance, plastic will almost always benefit from solvent-based ink that dries quickly, such as those made with methyl ethyl ketone (MEK).
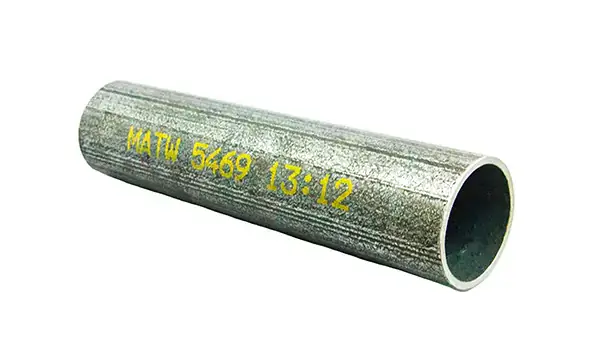
Sample marks such as this can help determine, among other factors, if the selected ink provides enough contrast for your application.
Sample marks and testing for the win
Once you’ve captured the requirements for your marking application, the next step in the ink selection process is to provide Matthews Marking Systems with sample products for testing and evaluation. This step is a critical part of the process and should never be skipped.
Testing samples under conditions and line speeds similar to your factory environment is essential when determining the optimal ink for you application. Doing so ensures that the chosen ink creates consistent marks and works reliably with your inkjet print technology.
The pitfalls of alternative ink suppliers
Before we wrap up, let’s take a moment to address why purchasing ink from a third-party other than your equipment supplier is not in your best interest.
Even though third-party ink may save a few dollars on ink costs, there is the real risk that such inks have not been tested with appropriate rigor on your specific printer under simulated factory conditions. Over time, this can cause problems; such as increased printhead clogging and wear. If this happens, you may spend more money in the long run due to increased maintenance expenses, decreased mark quality, and potentially unplanned stoppages. This is why purchasing ink as part of a complete inkjet marking solution will deliver the best quality, lowest overall cost, and most consistent marking results possible.
Chemical expertise is crucial to ink development
At Matthews Marking Systems, we’ve long recognized the vital role of ink in ensuring marking success. Our chemists and engineers have a combined 118 years of experience working in the ink industry. Offering research and development, ink production oversight, systems testing, sample marking, and technical support, this team has the experience and know-how to tackle your toughest marking challenges.
In addition, we can test inks as part of a complete solution with the Matthews print technology best suited for your application. This test ensures rock-solid reliability and the highest quality marks, lowering costs and improving overall performance. We look forward to putting our know-how to work for you. Contact us by filling out the form below to learn more.