Verify Twice, Ship Once: Using Barcode Verification to Reduce Errors, Save Money and Protect Your Reputation
We’ve all been there: patiently waiting in the checkout aisle as the employee passes your bag of bread or laundry detergent in attempt to scan the barcode. After several attempts and many sighs, the manual entry process begins.
Now imagine this on a much larger scale. Your pallet of products or large shipment arrives at your distributor’s warehouse. Poor printing, a coding error, or general readability issues have the receiving employee scanning the barcode a few times, then giving up. The patience experienced in the checkout aisle evaporates as that warehouse employee must scan hundreds or thousands of shipped goods every day. Your shipment is rejected, and this causes a ripple effect. Your bottom line takes a hit and the interruption in the supply chain process has significantly impacted your company’s reputation.
The best solution? Implement a barcode verification process into your production line. This verification objectively measures whether your barcodes meet ISO benchmarks for quality in terms of readability and scanning – and stays that way day in, day out. Barcode verifiers “grade” barcodes based on nine key factors, as established by the American National Standards Institute (ANSI), giving a score of either pass/fail or A-F for each category. After all nine have been evaluated, a total score is provided. According to Matthews Intelligent Identification, “while the target measurement for all barcodes is ISO Grade A, Grade B is often the acceptable minimum for 2D codes and Grade C for 1D codes.”
Why barcode verification should be on your radar
In addition to the impact on customers and your reputation, there are five other reasons to consider incorporating barcode verification into your manufacturing process:
Preparing for the future: Many industries and retailers, including automotive, transportation and logistics businesses, as well as medical and pharmaceutical companies, already require barcode verification from their vendors. In Australia, retailers like Coles, Metcash and Woolworths require GS1 barcode Verification Reports. It’s almost assured that all major distributors, wholesalers, manufacturers and retailers that are not currently mandating barcode verification will likely move in this direction by or before 2027 (in order to adhere to GS1’s Sunrise 2027 initiative). Failure to do so will result in a distinct competitive disadvantage.
Conforming to standards: Specifications for barcodes can vary by organization and industry, and this is especially true for government entities such as the FDA, DoD and EPA, which all have requirements for barcode grading and verification. Having a verification process established will allow you to better ensure that barcodes on your products are up-to-date and compliant with all standards.
Tracking your products: Traceability of products is critical these days and errors with coding can lead to delays, cancellations and recalls. Especially if you are in the food, beverage or pharmaceutical industries, errors with barcodes can make conducting a safe and effective recall almost impossible – putting both your reputation and the health and safety of your customers at risk.
Saving money: As alluded to above, there are few second chances granted by a retailer or distributor who cannot scan your products into their inventory. Errors almost always result in a negative financial impact to your company in the form of rejects, penalties and fines, and/or re-coding/re-shipping products. Proactively investing in a barcode verification system has a short-term financial impact, but the increased consistency and predictability
Ensuring readability under a range of conditions: While you can control your own production lines, there is no way to ensure that optimal conditions exist at the receiving end. As such, it’s imperative that barcodes on all of your products, boxes, and pallets meet the highest quality of standards so they pass muster at every single point. This means sharp contrast, crisp edges and accurate proportions.
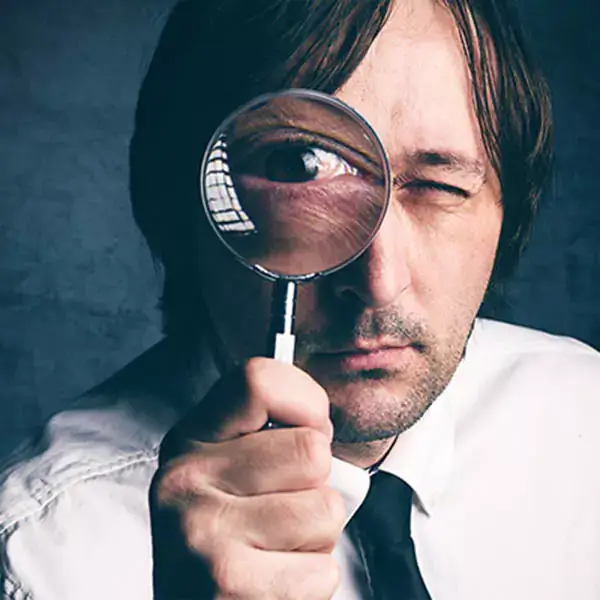
The nine key factors of verification
The idea with barcode verification is to catch errors early so they can be remedied before your products leave your warehouse. Ideally, of course, you won’t find any errors. It’s a learning process, and one advantage to using barcode verification is the ability to constantly improve your production operations over time. The best place to start is by understanding what a barcode verification system is looking for.
Here are the nine key attributes that are being evaluated in the verification process:
1. Edge determination (pass/fail): All barcodes must have the correct number of elements (bars and spaces) and they must all pass the minimum global threshold. Issues with ink bleeding can be a common reason for a “fail” grade with edge determination. The ink spreads and creates too narrow of a space for the verifier to read.
2. Minimum reflectance (pass/fail): Barcodes must be sufficiently dark enough for scanners to read, so this test measures the darkness of the bars, with the darkest bar having a reflectance that is 50% or less than that of the background and spaces. Using a darker ink or increasing resolution can resolve this issue.
3. Symbol contrast (A-F grade): The lower the contrast between bars and spaces, the higher the likelihood that scanners can’t tell the difference. This evaluation compares the highest and lowest reflectance values and determines if the difference will help or hinder readability.
4. Minimum edge contrast (pass/fail): This measurement looks at the smallest contrast value (e.g. narrow or lighter bars) between a bar and a space to ensure they can still be read by a scanner.
5. Modulation (A-F grade): Narrow spaces and bars can cause issues with readability because they do not have the same level of contrast as wider spaces and bars, and scanners may perceive the actual spaces as being narrower than they are. The modulation assessment ensures that any narrow elements are still distinct enough to be picked up by a scanner.
6. Defects (A-F grade): As you may have guessed, this measurement looks at any printing defects that may impact readability, specifically “voids” and “spots.” In essence this means bars with light areas and spaces with dark areas, both of which can “confuse” a scanner. Monitoring ink levels can help with voids and ensuring ink heads are properly cleaned can also help with these issues.
7. Quiet zone (pass/fail): Quiet zones are restricted areas on the right and left sides of the bar code which cannot contain any text or graphics. One common cause of a “fail” grade is printing too close to the edge of a box or product.
8. Decode (pass/fail): As part of the verification process, the verifier will decode the bar and spaces into numbers and characters. Essentially, this is checking that the barcode symbols have been coded correctly. While spots or other marks may impact the decoding score, it could also mean there is an issue with the coding equipment, which may impact other barcodes being used.
9. Decodability (A-F grade): As mentioned above, the verifier converts the bars and spaces into digits and other characters, and the decodability score measures how well a scanner can read those numbers. This relies on the thickness/width of each element being correct and, as with other categories, ink spread or issues with the graphics system can be culprits for a low score.
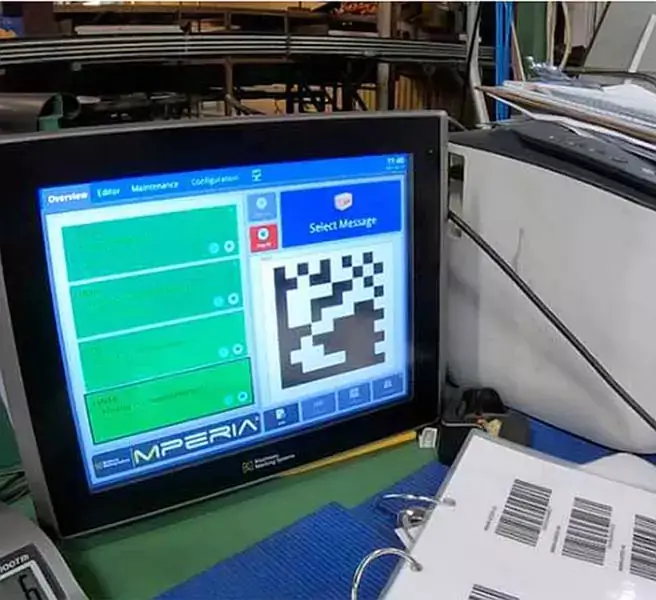
Though it may sound a bit daunting, the reality is that with the right technology in place, a verification process can easily be integrated in your existing systems so that you don’t ever have to lose sleep over improper coding or printing. From start to finish, Matthews’ MPERIA platform, our 2D barcode validation capabilities and our line of high-resolution thermal and piezo inkjet printers can help ensure that your products make it to their final destination without marking fails. As a universal print controller, MPERIA centralizes operations of your printers (including non-Matthews printers and laser marking systems), code verifiers, barcode readers, vision systems, scales and actuators. Visit our Barcode Verification and Printing page to learn more!