Fairview Swiss Cheese upgrades to Matthews’ MPERIA® L-Series thermal inkjet (TIJ) using LS-6101 ink (dye-based, fast-drying with FDA incidental contact approval) and gains seamless integration capabilities to improve efficiency, eliminate production stoppages, and reduce overall marking costs.
Industry: Food & Beverage
Application: Automated Marking
Products: MPERIA Controller, L-Series thermal inkjet (TIJ)
Summary
Fairview Swiss cheese is not only Pennsylvania’s largest manufacturer and retailer for Swiss cheese, it’s also a family-run business with an impressive legacy built by four generations of cheese makers. Over the decades, the company has grown from making four blocks of cheese (800 pounds) per day to producing more than seven million pounds of premium Swiss cheese per year. Their success story is driven by time-honored tradition combined with a commitment to seeking out and using the most modern and efficient equipment throughout their operations. They even use byproducts of the cheese-making process to generate green energy! Matthews Marking became part of their journey when they decided to replace their outdated print-and-apply solution with Matthews’ MPERIA® L-Series inkjet marking and coding solution. This allowed them to easily integrate their scale for weight coding, simplify the marking process, reduce consumable expenses, and eliminate a lot of production headaches.
The Challenge
Located in Fredonia, PA, Fairview Cheese is a proud, family-run business with four generations of history and a focus on forward-looking values including simplicity, quality, purity, and value. They are the only Swiss cheese plant in Pennsylvania, and they produce a premium product, which they sell direct to retail and wholesale customers up and down the Eastern seaboard. They reach customers further afield via large distributors with coast-to-coast coverage.
Fairview’s production line produces and packages an average of approximately 15,000 pounds of premium Swiss cheese per day. Their output includes a variety of cuts for different wholesale and retail customers. Each item is marked with weight, expiration date, and a lot number for traceability.
Prior to implementing the Matthews Marking solution, Fairview was using an outdated print-and-apply solution that did not meet their expectations in terms of either productivity or efficiency. For example, they frequently had to halt the production line in order to replace label stock, fix ribbon breakage, or resolve ribbon jams in the label applicator. Such stoppages created a domino effect that extended delays because the operator needed to ensure that any product that had already gone over the scale was properly queued up in the right order to ensure accurate weight labeling.
The Solution
Throughout their history, Fairview has always been committed to using the highest quality ingredients and most modern cheese-making equipment. This attention to detail and excellence extends to every aspect of their operation, including packaging, which is one of the reasons they chose to work with Matthews Marking when considering an upgrade. After evaluating Fairview’s production, Matthews recommended L-Series thermal inkjet (TIJ) printing with a MPERIA® controller. Though initially concerned about marking directly on the polywrap used to package their blocks of Swiss cheese, the use of Matthews’ LS-6101 dye-based, quick-drying black ink has FDA incidental contact approval removed any apprehension. In addition to optimizing efficiency, Fairview gained simplicity of operation, cost savings, easy implementation, advanced integration capabilities, and outstanding (and local) support.
Smoother Operations
The L-Series offers consistent, high-quality prints without the headaches often associated with other printing technologies. The system allows Fairview to keep its production line moving with virtually maintenance-free cartridge-based printheads that can be changed in mere seconds. Eliminating labels resolved a lot of issues.
“The MPERIA L-Series saves us a lot of headaches and makes everything a lot smoother from an operational standpoint,” says Michael Koller, VP of Finance at Fairview. “If we do run into any problems, it’s nothing to do with the MPERIA® controller or the L-Series printhead. It’s an issue on our end like something catching on the sensor.”
Lower Consumable and Other Costs
The Matthews’ inkjet solution also helped Fairview to substantially reduce consumable costs. Instead of having to spend $3000 to $4000 to maintain a month’s worth of label stock, they now spend only $260 per month, which includes a back-up ink cartridge just in case production ramps up unexpectedly.
In addition to the system being almost entirely maintenance free, the MPERIA solution eliminated line stoppages to resolve ribbon outages, breaks, and jams.
“The MPERIA® L-Series saves us a lot of time and money,” says Michael. “It makes things much more efficient.”
Uniquely Advanced Integration Capabilities
Fairview takes advantage of MPERIA®’s comprehensive integration features by seamlessly sending the weight data from the scale to the
MPERIA® controller for printing by the L-Series. This unique capability allows Fairview to feed weight data directly into the MPERIA® controller in real time as product moves down the line.
In addition, MPERIA®’s flexibility, scalability, and user-friendly interface make it easy for the Fairview team to make changes on the fly. “Anything to do with the MPERIA® controller — we can do right on the screen,” says Michael. “We can edit, add, or delete anything quickly and easily.” This makes it possible for Fairview to easily provide custom marking for specific customers.
Fast and Easy Implementation
Getting up and running with the new Matthews’ system was quick and simple, taking only a little over a day, including the integration with Fairview’s scales. “The team worked on getting the scale and MPERIA® communicating, and the next day we were running,” says Michael. “It was nothing complicated.”
Exceptional Support
Even though the Matthews’ system has been humming along without issue, Fairview still appreciates having reliable access to expert support. “We like that Matthews has a facility in Cranberry, so they aren’t far away,” says Michael. “They are easy to get hold of if we have questions. And if we ever need someone to come up, they can be here in a day or even a couple hours, which is great.”
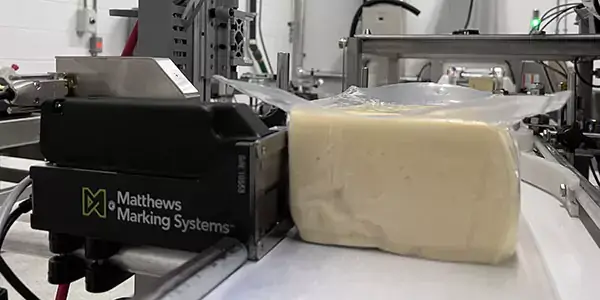
L-Series L12 marking packaged Swiss cheese block with LS-6101 FDA incidental approved ink.
The Results
With the new Matthews’ MPERIA® L-Series solution on their production line, Fairview has been able to achieve a greater level of simplicity and efficiency in their production line. They have been able to eliminate almost all of the issues that previously caused headaches and line stoppages, and they have gained substantial cost savings both in terms of consumables and overall productivity. “We are very satisfied,” says Michael. “The MPERIA® L-Series is a lot easier and simplifies a lot of things for us. It has solved problems and eliminated issues that we otherwise would have had.”
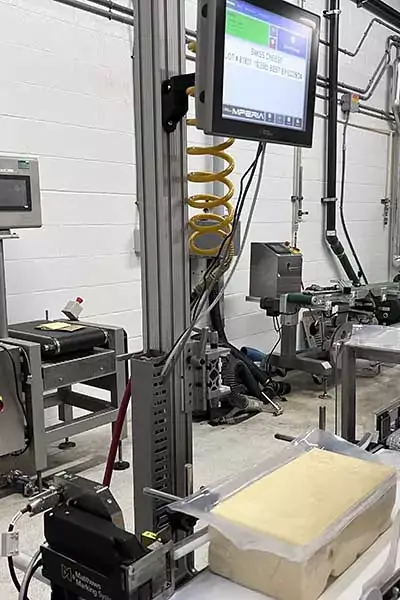
MPERIA 12″ controller driving the L12 after receiving weight data from the scale.
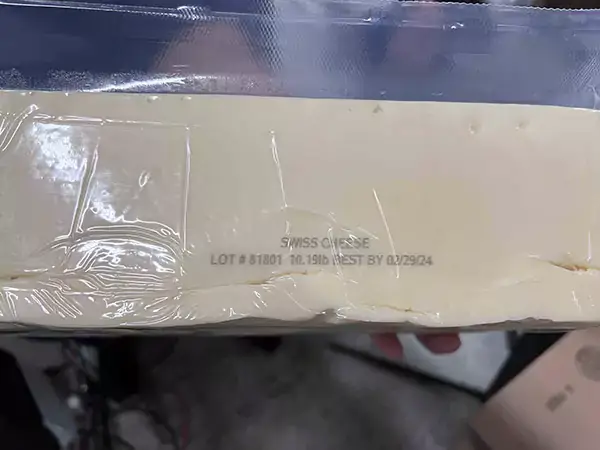
Product identification and traceability data printed by the MPERIA L12
About Fairview Swiss Cheese
Fairview Swiss Cheese is Pennsylvania’s largest Swiss cheese manufacturer and retailer. The family-owned company is celebrating four generations of cheese-makers, all of whom are committed to a vision based on the values of simplicity, quality, purity, and value. Fairview produces approximately seven million pounds of premium Swiss cheese each year, serving wholesalers and retailers up and down the Eastern seaboard and other customers further afield via national distributors. Fairview also contributes to a healthier planet for everyone by producing all of their cheese using green energy, including electricity they produce themselves by processing production byproducts using anaerobic digestion.