How Haley Manufacturing’s Gentle Bagger and Matthews’ MPERIA® L-Series Are Helping Fruit Packagers Transition from Manual Labor to Cutting-edge Automation
Industry: Food & Beverage
Application: Automated Marking
Products: MPERIA Controller, L-Series thermal inkjet (TIJ)
Summary
Located in Yakima, Washington, Haley Manufacturing is a world leader in high-quality packaging equipment and integration solutions, especially for delicate fruit products. They serve clients from coast to coast in North America, including Olympic Fruit, a packing operation founded by four multi-generational farming families. Olympic is committed to investing in the latest, industry-leading technology in order to deliver the best product to their customers. Haley helps Olympic keep this commitment by providing them with an integrated solution that combines their innovative gentle bagging equipment with Matthews Marking’s MPERIA® L-Series L12 Thermal Inkjet marking and coding solution. This combination of technology helps Olympic and other Haley customers reduce labor costs, increase productivity, and set them up for ongoing future growth and success.
The Challenge
The primary challenge for most fruit packaging operations is an over reliance on manual labor. Because fruit is such a fragile product, packagers have traditionally had to hand label each bag or pouch of product — a very time consuming and expensive process that also tends to slow down production because workers cannot usually match the speed of automated packaging equipment.
Hand labeling also contributes to other inefficiencies. For example, if a quantity of bags are hand labeled, but not filled on the same day, the label information becomes invalid. This means that the bags either have to be scrapped completely — increasing supply costs — or the labels have to be removed and replaced (again, by hand), which increases labor costs.
Packaging operations also have difficulty retaining well-trained staff to do the very repetitive and boring job of hand labeling produce bags.
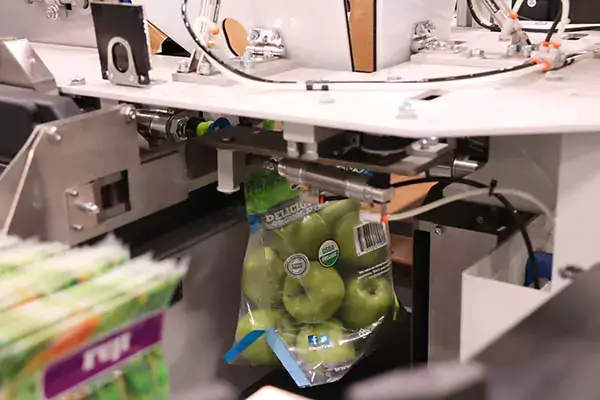
Apple pouch marked by L12 getting filled.
The Solution
Haley helps their customers overcome all the standard challenges with their automated poly (with quick-lock closure) and pouch (reclosable zipper) baggers. Although Haley is relatively new in the industry, they quickly assumed a leadership position amidst more established players by being the first to perfect the “gentle bagging” solution that packagers have been waiting for. Haley integrates their innovative baggers with Matthews’ MPERIA® L-Series inkjet marking and coding solution to provide an all-in-one solution that increases efficiency and productivity in both the bagging and marking areas.
Haley connects their automated baggers to batching systems, which are fed by different sizing, grading, or weighing units. Pre-ready bags go through a feed system, which sends them through the integrated L-Series printer. Once the bag has been printed — with whatever lot information, use-by date, barcodes, etc. are required — it is sent into the hopper and the fill area, opened, filled, sealed, and then discharged to an automatic weight-checking station before being sent on for boxing and palletization.
Haley chose to work with Matthews’ for many reasons, including:
The ability to control multiple print heads via one MPERIA® controller.
Other marking solutions are restricted to a 1:1 printer-to-bagger configuration, meaning that each time a lot or packed-on date changes, the operator has to update each printer separately. If the operation is running 30 baggers, that’s 30 manual changes, and a lengthy delay in production.
“With the MPERIA® L-Series, we’re controlling twenty to thirty print heads from a single interface,” says Jeremy Briskey, service manager for Haley. “This makes it way easier for the operator and has definitely helped our customers out a lot.”
A compact footprint that can fit almost anywhere.
“A lot of packing houses already have a lot of equipment,” says Cari Wickersham, a member of Haley’s sales and marketing team. “The fact that the Matthews’ solution is quite a bit smaller than any competitor helps when we have to put a bagger in a tight footprint.”
Fast and easy integration and an intuitive interface.
Speed is vital in any production scenario, so Haley’s customers really appreciate how quickly and easily the Haley/Matthews solution can be integrated into the packaging process. “It’s a quick ‘drop-in’ fit,” says Jeremy. “There’s no need to re-engineer things or do any field mounting, and the cabling was easy — we’re able to power the printer directly from our bagger.”
The mark flexibility and quality.
Speed doesn’t matter if quality has to suffer, but the Haley/Matthews solution allows customers to have the best of both worlds. “The MPERIA® L-Series gives us a really good print quality, even when we’re doing barcodes on a line where the bags are flying through at eight units per minute,” says Jeremy. “Even when the bags are a little wavy or not one hundred percent aligned, we still get an excellent mark.”
A great support team and strong working relationship.
The Haley team really appreciates the level of partnership provided by the Matthews’ team. “We love working locally, and the communication has been really good,” says Cari. “Everyone is super nice and easy to work with.”
An excellent overall value.
On top of top quality and great service, Haley also wanted to make sure they were getting a good deal. “It’s hard to beat the Matthews’ price point considering the reliability and quality of their products,” says Jeremy.
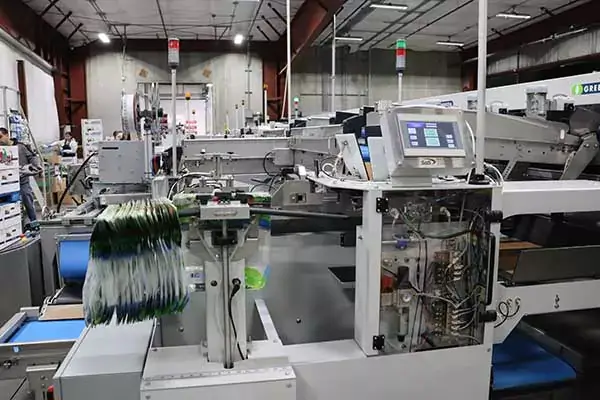
Haley’s automated bagger in action.
Olympic Fruit — One of Many Haley Success Stories
Olympic uses the Haley/Matthews bagging and marking solution in their Moxee, Washington facility where they store and pack thirteen apple varieties all year round — approximately 2 million apples per day. Their 78K-square foot production facility runs 6 pods — each of which includes two Haley pouch baggers and one poly bagger, and each bagger is integrated with a Matthews’ printer. Each of these pods processes approximately 11 tons of bagged apples per hour.
Like most delicate produce packaging operations, Olympic had been hand-applying stickers to their bags and had been dealing with all the challenges associated with that approach. With the Haley/Matthews solution, they have been able to automate their packaging process to improve efficiency and productivity.
The L-Series L12 Thermal Inkjet Printer is a right-fit solution for OEM integration that makes high-resolution marks of barcodes, lot codes, etc. on the pouches. Its cartridge-based printing delivers unbeatable uptime with cartridge swaps taking only seconds. And the MPERIA® controller allows operators to control multiple printheads from a single point that features a user-friendly and intuitive interface. The entire solution is designed to adapt to customer requirements rather than forcing customers to work within equipment constraints.
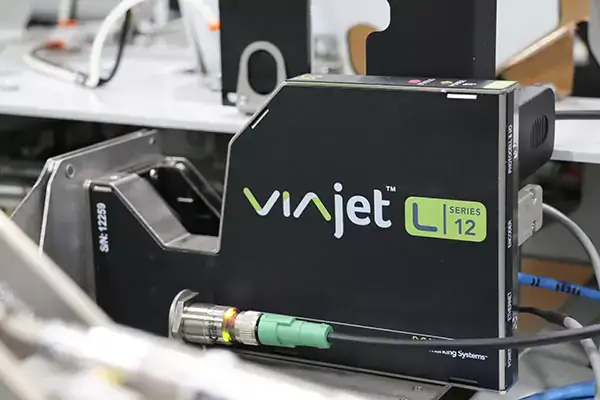
The Results
Haley’s experience with the Matthews’ integration has been overwhelmingly positive. “We’ve had a one hundred percent success rate putting the Matthews Marking system on our bagger,” says Jeremy, who also notes that almost all of their customers — 90% — take advantage of this all-in-one solution.
Haley’s customers are able to consistently reduce their labor costs, minimize product loss, and improve productivity. They are also universally impressed by the system’s flexibility and ability to quickly and easily adapt to address emerging packaging requirements like traceability and QR codes.
This integrated solution also offers Haley’s customers a strong ROI. “One automated pouch bagger can replace two or three individuals,” says Jeremy. “And when you add in the Matthews’ MPERIA® L-Series, that replaces at least another person who was previously hand labeling all the bags. So, the system pays for itself in a short amount of time.”
Olympic experienced these benefits first hand – increasing production by over 15%, which helped them project a 2.3 year ROI.
“Since putting in the Haley/Matthews equipment, we’ve reduced our labor and increased our throughput by about 15 ton an hour across our entire production operation,” says Robert Poteet, facility manager at Olympic Fruit. “We needed to be able to pack more product in an eight-hour shift, and the automation equipment gave us the flexibility to pack an additional 30,000 bins per year without adding additional shifts or overtime hours. That is big for us. The technology behind the MPERIA® controller is pretty impressive.”
About Haley Manufacturing
Haley Manufacturing is an original equipment manufacturer specializing in automated packing equipment for produce. Headquartered in Yakima, Washington, Haley is a world leader in providing the highest quality automated solutions for bagging, weighing, tray packing, and general produce handling and integration. They supply complete solutions that include design, manufacturing, integration, and service, and they take pride in having the experience and agility to consistently accommodate customers’ changing needs to reduce labor, increase throughput, and improve efficiency.
About Olympic Fruit Company, LLC
Located in Moxee, Washington, Olympic Fruit began as the vision of four, multi-generational farming families (Smith Family, Gamache Family, Charron Family and Carpenter Family) to provide its owners with a means of controlling both the packing and marketing of their apples. In 1999, Olympic Fruit joined forces with two other packing facilities in the Yakima area to form Sage Fruit Company. The operation is situated on 30 acres of land with over 175,000 square feet of production and inventory storage, and has enjoyed growth at twice the annual industry rate since 2000.